机械加工技术革新与效率提升策略
2024/11/9 15:12:36
机械加工技术革新与效率提升是制造业持续关注的重要议题,以下是一些相关策略:
一、技术革新策略
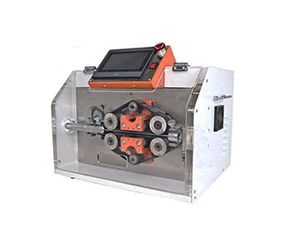
- 自动化技术的引入
- 数控加工(CNC)技术:数控加工技术是机械加工自动化的关键。它通过计算机程序控制机床的运动和加工过程。例如,在铣削复杂形状的零件时,传统机床需要经验丰富的工人手动操作,调整刀具路径和切削参数,而数控铣床可以根据预先编写好的程序地完成加工。这不仅提高了加工精度,还能实现复杂形状零件的批量生产。
- 工业机器人应用:工业机器人可以用于物料搬运、上下料等环节。比如在汽车零部件加工中,机器人可以将毛坯零件准确地放置到加工机床的工作台上,加工完成后再将成品取下,减少了人工操作的时间和劳动强度,同时提高了生产的安全性和稳定性。
- 制造工艺的采用
- 3D 打印技术:3D 打印也称为增材制造,是一种新兴的制造技术。它通过逐层堆积材料来制造零件。对于一些具有复杂内部结构的零件,如航空航天领域的轻量化结构件,3D 打印可以实现传统加工方法难以达到的设计。与传统的减材制造相比,3D 打印可以大大减少材料浪费,并且能够快速制造出原型或小批量的产品。
- 精密和超精密加工技术:在电子、光学等领域,对零件的精度要求高。精密和超精密加工技术能够实现纳米级甚至原子级的加工精度。例如,在制造计算机芯片时,需要使用光刻等精密加工技术,将电路图案地制作在硅片上,以确保芯片的高性能和可靠性。
- 智能化技术的融合
- 智能制造系统(IMS):智能制造系统将人工智能、物联网等技术融入机械加工。通过在机床上安装传感器,可以实时监测机床的状态,如温度、振动、刀具磨损等。利用人工智能算法对这些数据进行分析,能够预测设备故障,提前进行维护,减少停机时间。例如,通过分析刀具磨损的数据,系统可以自动调整切削参数或者提醒更换刀具,保证加工质量的稳定。
- 大数据与质量控制:收集机械加工过程中的大量数据,包括原材料特性、加工参数、成品质量检测结果等。利用大数据分析可以发现质量问题的根源,优化加工工艺。例如,在一批轴类零件加工中,通过分析加工尺寸偏差的数据,发现是由于某一时间段的切削液温度变化导致的,从而可以采取相应的措施来控制切削液温度,提高加工质量。
二、效率提升策略
- 优化加工工艺路线
- 工艺规划与仿真:在加工前,利用计算机辅助工艺规划(CAPP)软件对加工工艺进行详细规划。通过工艺仿真,可以验证工艺路线的合理性,避免加工过程中的干涉和错误。例如,在复杂模具加工中,通过仿真可以确定的粗加工、半精加工和精加工顺序,以及刀具的选择和切削参数,从而减少加工时间和成本。
- 并行加工与成组技术:对于一些可以同时进行加工的工序,采用并行加工方式。成组技术则是将相似的零件归为一组,采用相同的加工工艺和设备进行加工。这样可以提高设备利用率,减少换刀和调整设备的时间。例如,在机械加工车间,将形状相似的轴类零件归为一组,统一安排在车床上加工,提高了车床的生产效率。
- 刀具和切削参数优化
- 刀具材料与几何形状优化:选择合适的刀具材料,如硬质合金、陶瓷等,可以提高刀具的耐磨性和切削性能。同时,优化刀具的几何形状,如前角、后角、刃口半径等,可以降低切削力,提高切削效率。例如,在高速切削时,采用具有特殊刃口形状的刀具,可以有效减少切削热的产生,提高加工表面质量。
- 切削参数的智能调整:根据加工材料、刀具和机床性能等因素,合理确定切削速度、进给量和切削深度。并且利用自适应控制技术,在加工过程中根据实际情况自动调整切削参数。例如,当切削力增大时,自动降低进给量,以保证加工过程的稳定性和零件质量。
- 人员培训与管理
- 员工技能提升:定期对机械加工操作人员进行技能培训,包括新设备操作、新工艺应用等方面。熟练的员工能够更快、更准确地完成加工任务。例如,通过培训员工掌握数控编程和操作技能,可以充分发挥数控设备的优势,提高加工效率。
- 团队协作与激励机制:在机械加工车间,建立良好的团队协作氛围,加强不同工序之间员工的沟通与协作。同时,设立合理的激励机制,如绩效奖金、技能竞赛奖励等,激发员工的工作积性和创造力,从而提高整体生产效率。